Chip production rate and tool wear estimation in micro-endmilling
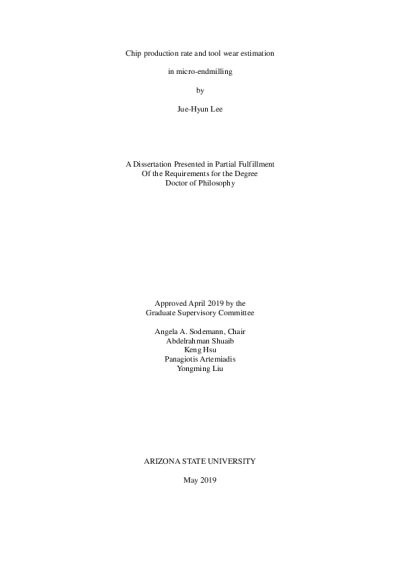
Description
In this research, a new cutting edge wear estimator for micro-endmilling is developed and the reliabillity of the estimator is evaluated. The main concept of this estimator is the minimum chip thickness effect. This estimator predicts the cutting edge radius by detecting the drop in the chip production rate as the cutting edge of a micro- endmill slips over the workpiece when the minimum chip thickness becomes larger than the uncut chip thickness, thus transitioning from the shearing to the ploughing dominant regime. The chip production rate is investigated through simulation and experiment. The simulation and the experiment show that the chip production rate decreases when the minimum chip thickness becomes larger than the uncut chip thickness. Also, the reliability of this estimator is evaluated. The probability of correct estimation of the cutting edge radius is more than 80%. This cutting edge wear estimator could be applied to an online tool wear estimation system. Then, a large number of cutting edge wear data could be obtained. From the data, a cutting edge wear model could be developed in terms of the machine control parameters so that the optimum control parameters could be applied to increase the tool life and the machining quality as well by minimizing the cutting edge wear rate.
In addition, in order to find the stable condition of the machining, the stabillity lobe of the system is created by measuring the dynamic parameters. This process is needed prior to the cutting edge wear estimation since the chatter would affect the cutting edge wear and the chip production rate. In this research, a new experimental set-up for measuring the dynamic parameters is developed by using a high speed camera with microscope lens and a loadcell. The loadcell is used to measure the stiffness of the tool-holder assembly of the machine and the high speed camera is used to measure the natural frequency and the damping ratio. From the measured data, a stability lobe is created. Even though this new method needs further research, it could be more cost-effective than the conventional methods in the future.
In addition, in order to find the stable condition of the machining, the stabillity lobe of the system is created by measuring the dynamic parameters. This process is needed prior to the cutting edge wear estimation since the chatter would affect the cutting edge wear and the chip production rate. In this research, a new experimental set-up for measuring the dynamic parameters is developed by using a high speed camera with microscope lens and a loadcell. The loadcell is used to measure the stiffness of the tool-holder assembly of the machine and the high speed camera is used to measure the natural frequency and the damping ratio. From the measured data, a stability lobe is created. Even though this new method needs further research, it could be more cost-effective than the conventional methods in the future.
Date Created
The date the item was original created (prior to any relationship with the ASU Digital Repositories.)
2019
Agent
- Author (aut): Lee, Jue-Hyun
- Thesis advisor (ths): SODEMANN, ANGELA A
- Committee member: Shuaib, Abdelrahman
- Committee member: Hsu, Keng
- Committee member: Artemiadis, Panagiotis
- Committee member: Liu, Yongming
- Publisher (pbl): Arizona State University