Fatigue Life Prediction Using Hybrid Prognosis for Structural Health Monitoring
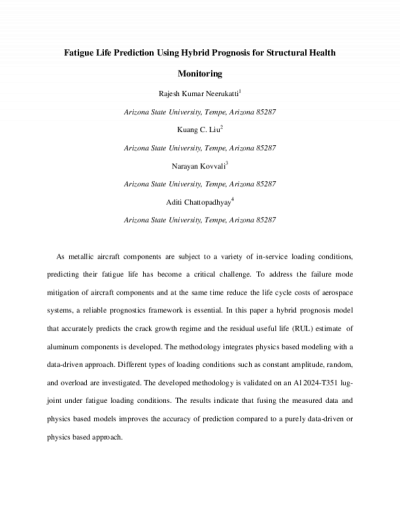
Description
Because metallic aircraft components are subject to a variety of in-service loading conditions, predicting their fatigue life has become a critical challenge. To address the failure mode mitigation of aircraft components and at the same time reduce the life-cycle costs of aerospace systems, a reliable prognostics framework is essential. In this paper, a hybrid prognosis model that accurately predicts the crack growth regime and the residual-useful-life estimate of aluminum components is developed. The methodology integrates physics-based modeling with a data-driven approach. Different types of loading conditions such as constant amplitude, random, and overload are investigated. The developed methodology is validated on an Al 2024-T351 lug joint under fatigue loading conditions. The results indicate that fusing the measured data and physics-based models improves the accuracy of prediction compared to a purely data-driven or physics-based approach.
Date Created
The date the item was original created (prior to any relationship with the ASU Digital Repositories.)
2014-04-01
Agent
- Author (aut): Neerukatti, Rajesh Kumar
- Author (aut): Liu, Kuang C.
- Author (aut): Kovvali, Narayan
- Author (aut): Chattopadhyay, Aditi
- Contributor (ctb): Ira A. Fulton Schools of Engineering
- Contributor (ctb): School for the Engineering of Matter, Transport and Energy