A study on an in-process laser localized pre-deposition heating approach to reducing FDM part anisotropy
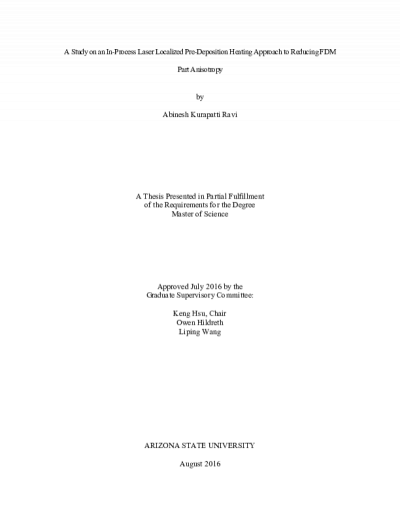
Description
Material extrusion based rapid prototyping systems have been used to produceprototypes for several years. They have been quite important in the additive manufacturing field, and have gained popularity in research, development and manufacturing in a wide field of applications. There has been a lot of interest in using these technologies to produce end use parts, and Fused Deposition Modeling (FDM) has gained traction in leading the transition of rapid prototyping technologies to rapid manufacturing. But parts built with the FDM process exhibit property anisotropy. Many studies have been conducted into process optimization, material properties and even post processing of parts, but were unable to solve the strength anisotropy issue. To address this, an optical heating system has been proposed to achieve localized heating of the pre- deposition surface prior to material deposition over the heated region. This occurs in situ within the build process, and aims to increase the interface temperature to above glass transition (Tg), to trigger an increase in polymer chain diffusion, and in extension, increase the strength of the part. An increase in flexural strength by 95% at the layer interface has been observed when the optical heating method was implemented, thereby improving property isotropy of the FDM part. This approach can be designed to perform real time control of inter-filament and interlayer temperatures across the build volume of a part, and can be tuned to achieve required mechanical properties.
Date Created
The date the item was original created (prior to any relationship with the ASU Digital Repositories.)
2016
Agent
- Author (aut): Kurapatti Ravi, Abinesh
- Thesis advisor (ths): Hao Hsu, Keng
- Committee member: Hildreth, Owen
- Committee member: Wang, Liping
- Publisher (pbl): Arizona State University