The development and engineering application of a fiber reinforced hybrid matrix composite for structural retrofitting and damage mitigation
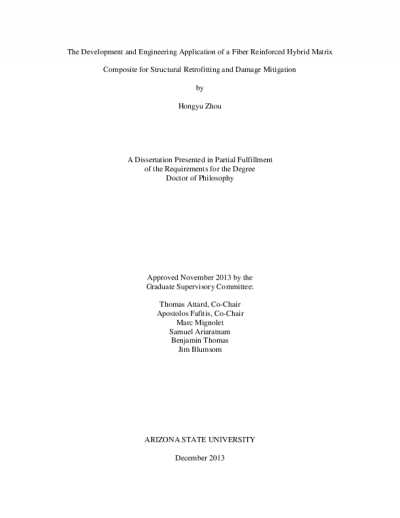
Description
Civil infrastructures are susceptible to damage under the events of natural or manmade disasters. Over the last two decades, the use of emerging engineering materials, such as the fiber-reinforced plastics (FRPs), in structural retrofitting have gained significant popularity. However, due to their inherent brittleness and lack of energy dissipation, undesirable failure modes of the FRP-retrofitted systems, such as sudden laminate fracture and debonding, have been frequently observed. In this light, a Carbon-fiber reinforced Hybrid-polymeric Matrix Composite (or CHMC) was developed to provide a superior, yet affordable, solution for infrastructure damage mitigation and protection. The microstructural and micromechanical characteristics of the CHMC was investigated using scanning electron microscopy (SEM) and nanoindentation technique. The mechanical performance, such as damping, was identified using free and forced vibration tests. A simplified analytical model based on micromechanics was developed to predict the laminate stiffness using the modulus profile tested by the nanoindentation. The prediction results were verified by the flexural modulus calculated from the vibration tests. The feasibility of using CHMC to retrofit damaged structural systems was investigated via a series of structural component level tests. The effectiveness of using CHMC versus conventional carbon-fiber reinforced epoxy (CF/ epoxy) to retrofit notch damaged steel beams were tested. The comparison of the test results indicated the superior deformation capacity of the CHMC retrofitted beams. The full field strain distributions near the critical notch tip region were experimentally determined by the digital imaging correlation (DIC), and the results matched well with the finite element analysis (FEA) results. In the second series of tests, the application of CHMC was expanded to retrofit the full-scale fatigue-damaged concrete-encased steel (or SRC) girders. Similar to the notched steel beam tests, the CHMC retrofitted SRC girders exhibited substantially better post-peak load ductility than that of CF/ epoxy retrofitted girder. Lastly, a quasi-static push over test on the CHMC retrofitted reinforced concrete shear wall further highlighted the CHMC's capability of enhancing the deformation and energy dissipating potential of the damaged civil infrastructure systems. Analytical and numerical models were developed to assist the retrofitting design using the newly developed CHMC material.
Date Created
The date the item was original created (prior to any relationship with the ASU Digital Repositories.)
2013
Agent
- Author (aut): Zhou, Hongyu
- Thesis advisor (ths): Attard, Thomas L
- Thesis advisor (ths): Fafitis, Apostolos
- Committee member: Mignolet, Marc P
- Committee member: Ariaratnam, Samuel
- Committee member: Thomas, Benjamin
- Committee member: Blumsom, Jim
- Publisher (pbl): Arizona State University