Implementation of a Coupled Creep Damage Model in MOOSE Finite Element Framework: Application to Irradiated Concrete Structures
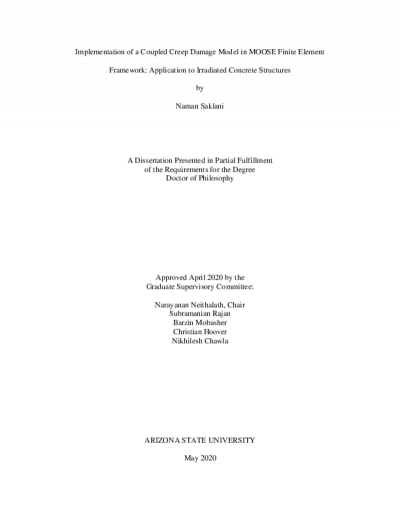
Description
There has been a renewed interest to understand the degradation mechanism of concrete under radiation as many nuclear reactors are reaching their expiration date. Much of the information on the degradation mechanism of concrete under radiation comes from the experiments, which are carried out on very small specimens. With the advent of finite element analysis, a numerical predictive tool is desired that can predict the extent of damage in the nuclear concrete structure.
A mesoscale micro-structural framework is proposed in Multiphysics Object-Oriented Simulation Environment (MOOSE) finite element framework which represents the first step in this direction. As part of the framework, a coupled creep damage algorithm was developed and implemented in MOOSE. The algorithm considers creep through rheological models, while damage evolves exponentially as a function of elastic strain and creep strain. A characteristic length is introduced in the formulation such that the energy release rate associated with each element remains the same to avoid vanishing energy dissipation with mesh refinement. A creep damage parameter quantifies the effect of creep strain on the damage that was calibrated using three-point bending experiments with varying rates of loading.
The creep damage model was also validated with restrained ring shrinkage tests on cementitious materials containing compliant/stiff inclusions subjected to variable drying conditions. The simulation approach explicitly considers: (i) moisture diffusion driven differential shrinkage along the depth of the specimen (ii) viscoelastic response of aging cementitious materials (iii) isotropic damage model with Rankine′s failure initiation criterion, and (iv) random distribution of tensile strengths of individual finite elements.
The model was finally validated with experimental results on neutron-irradiated concrete. The simulation approach considers: (i) coupled hygro-thermal model to predict the temperature and humidity profile inside the specimen (ii) radiation-induced volumetric expansion of aggregates (RIVE) (iii) thermal, shrinkage and creep effects based on the temperature and humidity profile and (iv) isotropic damage model with Rankine’s criterion to determine failure initiation.
A mesoscale micro-structural framework is proposed in Multiphysics Object-Oriented Simulation Environment (MOOSE) finite element framework which represents the first step in this direction. As part of the framework, a coupled creep damage algorithm was developed and implemented in MOOSE. The algorithm considers creep through rheological models, while damage evolves exponentially as a function of elastic strain and creep strain. A characteristic length is introduced in the formulation such that the energy release rate associated with each element remains the same to avoid vanishing energy dissipation with mesh refinement. A creep damage parameter quantifies the effect of creep strain on the damage that was calibrated using three-point bending experiments with varying rates of loading.
The creep damage model was also validated with restrained ring shrinkage tests on cementitious materials containing compliant/stiff inclusions subjected to variable drying conditions. The simulation approach explicitly considers: (i) moisture diffusion driven differential shrinkage along the depth of the specimen (ii) viscoelastic response of aging cementitious materials (iii) isotropic damage model with Rankine′s failure initiation criterion, and (iv) random distribution of tensile strengths of individual finite elements.
The model was finally validated with experimental results on neutron-irradiated concrete. The simulation approach considers: (i) coupled hygro-thermal model to predict the temperature and humidity profile inside the specimen (ii) radiation-induced volumetric expansion of aggregates (RIVE) (iii) thermal, shrinkage and creep effects based on the temperature and humidity profile and (iv) isotropic damage model with Rankine’s criterion to determine failure initiation.
Date Created
The date the item was original created (prior to any relationship with the ASU Digital Repositories.)
2020
Agent
- Author (aut): Saklani, Naman
- Thesis advisor (ths): Neithalath, Narayanan
- Committee member: Rajan, Subramanian
- Committee member: Mobasher, Barzin
- Committee member: Hoover, Christian
- Committee member: Chawla, Nikhilesh
- Publisher (pbl): Arizona State University